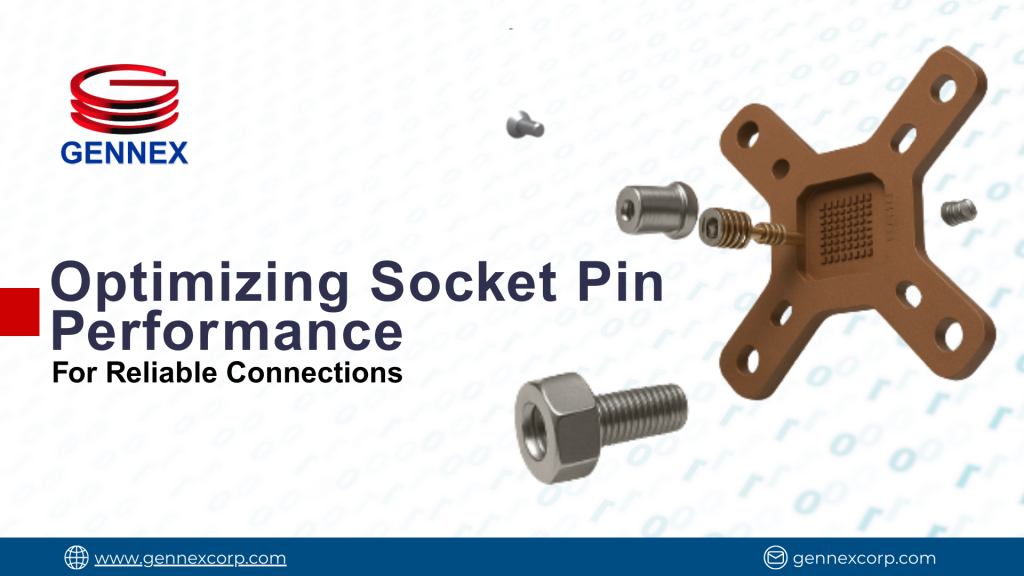
Socket Pin
SOCKET PIN – As you design and manufacture electronic devices, the importance of reliable connections cannot be overstated. Socket pins play a crucial role in ensuring consistent electrical contact between components. However, manufacturers do not create all socket pins equally.
To improve performance and reduce failures, carefully consider factors like material choice, plating options, and pin geometry.
Understanding Socket Pins: Construction and Function
Socket pins are crucial components in electrical and electronic connections, serving as the interface between devices and circuit boards. These small but mighty conductors play a vital role in ensuring reliable power and signal transmission.
Where to get high quality Socket Pins for your application?
Optimizing socket pin performance is crucial for ensuring reliable connections in electronic devices and systems. Implementing proper design practices, conducting thorough testing, and adhering to industry standards will further improve pin reliability.
Gennex offers durable and precision-engineered socket pins ideal for demanding electronic and industrial uses, backed by trusted global brands and local technical support
Anatomy Of A Socket Pin
At its core, a socket pin consists of three main parts:
- Contact area: The exposed metal surface that makes physical contact with the mating component.
- Body: The main structure of the pin, often made of conductive materials like copper alloys.
- Termination: The end that connects to the circuit board or wire.
(Socket pins come in various shapes and sizes, each designed for specific applications.)
Functional Mechanisms
Socket pins rely on several key principles to maintain optimal connections:
- Spring action: Many socket pins incorporate a spring mechanism to ensure consistent contact pressure.
- Surface finish: Gold or tin plating enhances electrical performance and corrosion resistance.
- Wiping action: The insertion and removal process helps clean contact surfaces, improving long-term reliability.
Understanding these construction elements and functional mechanisms is essential for engineers and technicians working with socket pins. Choosing the right pin type and design for an application can greatly improve the performance and lifespan.
Factors Affecting Socket Pin Performance
Socket pin performance is crucial for ensuring reliable electrical connections in various applications. Several key factors influence how well these pins function and maintain connection over time.
Optimizing Socket Pin Design for Reliable Connections
Geometric Considerations
The shape and dimensions of socket pins play a vital role in their reliability. A tapered design can facilitate easier insertion and removal while maintaining a secure fit. Pay attention to the contact surface area, as larger surfaces generally provide better electrical connections.
However, balance this with the need for compact designs in modern electronics. Precision manufacturing techniques ensure tight tolerances, reducing the risk of misalignment or poor contact.
Surface Treatment
To enhance electrical performance and protect against oxidation, surface treatments are essential. Gold plating is a popular choice for its excellent electrical performance and corrosion resistance. For more cost-effective solutions, nickel or tin plating can offer good performance in less demanding applications. Consider selective plating techniques to optimize material usage and reduce costs without compromising on critical contact areas.
Testing and Validation
Rigorous testing is crucial to ensure socket pin reliability. Implement cyclic durability tests to simulate repeated insertions and removals. Conduct environmental stress tests, including thermal cycling and humidity exposure, to verify performance under various conditions. Electrical testing should include resistance measurements and signal integrity to confirm optimal electrical performance and minimal interference.
Material
When designing socket pins for optimal performance, selecting the right materials is crucial. Designers often prefer high-performance metals like copper alloys or gold-plated contacts for their excellent electrical performance. These materials minimize signal loss and ensure consistent connections over time. Additionally, consider the environmental factors the socket will face, such as temperature fluctuations or corrosive atmospheres, to choose materials with appropriate durability and resistance.
Ensuring Proper Socket Pin Installation and Maintenance
Boosting Socket Pin Durability: Materials and Coatings
Advanced Alloys for Enhanced Performance
Socket pin durability is crucial for maintaining reliable connections in electronic devices. Manufacturers are increasingly turning to advanced alloys to improve pin strength and longevity. Copper alloys, such as beryllium copper and phosphor bronze, offer excellent electrical performance and spring properties.
Protective Coatings: The First Line of Defense
To further enhance durability, socket pins often receive specialized coatings. Gold plating remains a popular choice because to its excellent electrical performance and corrosion resistance. However, new coating technologies are emerging to offer cost-effective alternatives.
Nickel-palladium-gold (Ni-Pd-Au) coatings offer similar benefits to gold plating but at a lower cost. For applications requiring extreme wear resistance, hard gold or rhodium plating can significantly extend pin lifespan.
The Future of Socket Pins
Carbon nanotubes and graphene-based composites show promise in creating ultra-durable pins with exceptional electrical and mechanical properties. These materials could Transform socket design, enabling higher pin densities and improved reliability in harsh environments. As technology advances, we can expect to see these innovative materials making their way into commercial socket pin applications.
Sustainable Socket Pin Manufacturing
As the electronics industry evolves, there is a growing emphasis on sustainable manufacturing practices. Socket pin producers are exploring eco-friendly processes and materials to reduce their environmental footprint.
One promising approach is the use of recycled metals in socket pin alloys. Additionally, some companies adopt closed-loop manufacturing systems that recycle and reuse waste materials from the production process, minimizing waste and promoting resource efficiency.
Quality Control and Reliability Testing
To ensure consistent performance and durability, socket pin manufacturers employ rigorous quality control measures and reliability testing protocols. These may include:
- Dimensional inspections to verify pin geometry and tolerances
- Electrical testing to assess electrical performance and signal integrity
- Environmental stress tests to simulate harsh operating conditions
- Enhanced life cycle testing to evaluate long-term performance
By testing socket pins, manufacturers can spot and fix problems, ensuring their products meet quality standards and perform reliably.
As technology advances, socket pins will be key for strong, high-density connections in electronic devices.
As technology continues to advance, staying informed about the latest developments in socket pin technology will be essential. Improving socket pin perfomance can minimize connection failures, cut maintenance costs, and deliver more reliable products to your customers.